The company also builds essential ground-running equipment on the Stratasys Fortus 450mc 3D printer in tough Nylon 12 material at lower cost than aluminum production
MINNEAPOLIS & REHOVOT, Israel — (BUSINESS WIRE) — June 7, 2019 — Marshall Aerospace and Defence Group is now using advanced 3D printing from Stratasys (Nasdaq: SSYS) to manufacture, flight-ready parts for several of its military, civil and business aircraft - while producing specific ground-running equipment at a lower cost than aluminum alternatives. The company is currently one of the world’s largest privately owned and independent aerospace and defense companies.
This press release features multimedia. View the full release here: https://www.businesswire.com/news/home/20190607005013/en/
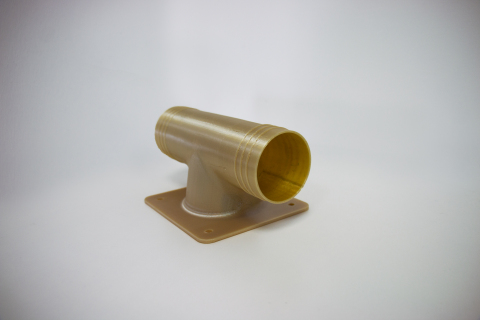
Final, flight-approved, 3D printed ducting for air conditioners. 3D printed in ULTEM™ 9085 resin on the Fortus 450mc (Photo: Business Wire)
Marshall already has several pieces of 3D-printed ductwork flying on heavily modified aircraft, as well as holders for safety knives and switches for aircraft interiors. 3D printing flight-approved parts on demand enables the company to produce lighter parts than traditional methods, significantly faster and at lower cost.
According to Chris Botting, Materials, Processes and Additive Manufacturing Engineer at Marshall ADG, the ability to create accurate, repeatable and reliable 3D printed parts using aerospace-approved materials are key factors in achieving the performance requirements necessary for use within aircraft.
“When manufacturing on complex engineering programs, we need a method that can create an accurate, complex, functional and lightweight duct efficiently with minimal tooling costs – this is where 3D printing fits perfectly. But we also need to ensure that the ducting work produced will be approved by the EASA for flight,” explains Botting. “As a result, we’re using the Stratasys Fortus 450mc FDM Printer and ULTEM™ 9085 resin – a tough, yet lightweight 3D printing material with high thermal and chemical resistance. This has been crucial to overcoming the stringent requirements of our industry, as we can now 3D print parts with the desired flame, smoke and toxicity properties for use on aircraft interiors.”
On the Ground Savings
The company is also utilizing its Fortus 450mc 3D printer, purchased from Stratasys UK and Ireland Platinum Partner SYS Systems, to build final parts on the ground. Marshall recently created a ducting adapter prototype for vital ground-running equipment – essential for providing fresh air to cool the aircraft’s avionics. 3D printing this particular part helped Marshall transition from typically costly aluminum processes.
“Before committing to expensive aluminum machining, we used the Fortus 450mc to 3D print a prototype in ASA material,” says Botting. “It enabled us to create an accurate working prototype of a complex component. We were then able to demonstrate it had the potential to be 3D printed in Nylon 12 material as opposed to the more conventional method of machining from aluminum. The 3D printed duct led to a significant cost reduction compared to machining the part out of aluminum, as well as a 63% reduction in overall weight.”
The group is also using Stratasys 3D printers for a range of complex tooling applications, including drill jigs, masking templates, bonded fixtures and composite mold tooling. The team regularly produces customized, low-volume production tools within just 24 hours of an engineer’s request. In fact, they are driving use of 3D-printed thermoplastic tools to replace heavy metal tools, reducing the burden on the operator, and crucially, reducing cost and lead times on urgent operational tasks.
Botting foresees the use of Stratasys FDM additive manufacturing to increase across all elements of the business and to drive new applications.
“FDM technology has altered the way we work, and the aerospace-grade 3D printers and materials enable us to meet our increasingly aggressive deadlines and complex manufacturing requirements,” Botting said. “In the future, there is no doubt that 3D printing will continue to have a significant impact in the way we design and manufacture in our business.”
To learn more about Stratasys’ additive manufacturing solutions for the aerospace industry, visit Hall 4, Stand D192 at the International Paris Air Show, 2019, June 17th – 23rd, Paris, France.
Marshall Aerospace and Defence Group has specialised in protecting people in critical situations for more than 100 years. Today the company continues to deliver world-leading applied engineering services to a wide range of global customers, ensuring they benefit from our agility, innovation and collaborative approach, whatever their needs. They rely on our core capabilities of managed services, integration and technologies, which we deliver in partnership through the ability to solve the most complex of challenges. We are a team of more than 1,800 highly skilled colleagues, located across UK, Canada, Europe and UEA, dedicated to setting the highest standards across the industry. Marshall Aerospace and Defence Group is part of Marshall of Cambridge (Holdings) Limited, the private holding company of the Marshall family. Founded in 1909, the Group had a turnover of nearly £2.5bn in 2018, and more than 6,000 employees.
Stratasys is a global leader in additive manufacturing or 3D printing technology and is the manufacturer of FDM® and PolyJet™ 3D printers. The company’s technologies are used to create prototypes, manufacturing tools, and production parts for industries, including aerospace, automotive, healthcare, consumer products and education. For 30 years, Stratasys products have helped manufacturers reduce product-development time, cost, and time-to-market, as well as reduce or eliminate tooling costs and improve product quality. The Stratasys 3D printing ecosystem of solutions and expertise includes: 3D printers, materials, software, expert services, and on-demand parts production. Online at: www.stratasys.com, http://blog.stratasys.com and LinkedIn.
Stratasys, FDM and Fortus are registered trademarks of Stratasys Inc. Fortus 450mc is a trademark of Stratasys, Inc. ULTEM™ is a registered trademark of SABIC or its affiliates. All other trademarks are the property of their respective owners, and Stratasys assumes no responsibility with regard to the selection, performance, or use of these non-Stratasys products.
Attention Editors, if you publish reader-contact information, please use:
- USA +800-801-6491
- Europe/Middle East/Africa +49-7229-7772-0
- Asia Pacific +852 3944-8888
View source version on businesswire.com: https://www.businesswire.com/news/home/20190607005013/en/
Contact:
Stratasys Media Contacts
Stratasys Corporate & North America
Email Contact
+1
612-364-3208
Europe, Middle East, and Africa
Jonathan Wake / Miguel
Afonso, Incus Media
Email Contact
+44
1737 215200
Greater China, Southeast Asia, ANZ and India
Alice Chiu
Email Contact
Japan and Korea
Email Contact
+81
3 5542 0042
Mexico, Caribe
Email Contact
00+52
(55) 15349791
Brazil, Central America and South America
Email Contact
+55
(11) 2626-9229
Marshall Aerospace Media Contact
Liz Fullick
PR Manager
Email Contact
+44
(0) 7825 357148
+44 (0) 1223 373865