-Realizes motor control with two dry-cell batteries-
TOKYO — (BUSINESS WIRE) — May 22, 2018 — Toshiba Electronic Devices & Storage Corporation today announced the launch of "TC78H651FNG,” a dual-H-bridge[1] driver IC for DC brushed motors and stepping motors that delivers the low voltage (1.8V) and high current (1.6A)[2] essential for low voltage equipment powered by dry-cell batteries, such as mobile devices, electronic products for the home and USB drives. Sample shipments start today.
This press release features multimedia. View the full release here: https://www.businesswire.com/news/home/20180522006519/en/
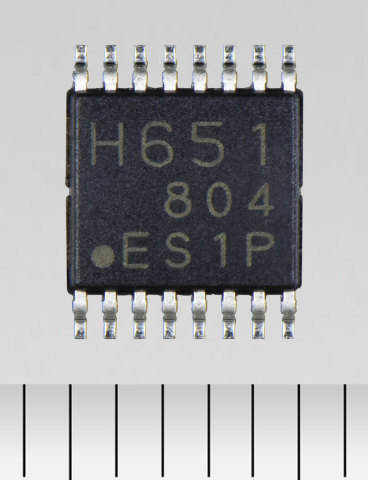
Toshiba: A dual-H-bridge driver IC "TC78H651FNG" for DC brushed motors and stepping motors that delivers the low voltage (1.8V) and high current (1.6A). (Photo: Business Wire)
In recent years, as IoT advances and wireless technologies find increasingly wide use, demand for applications that can be remotely operated via smartphones and other tools is increasing, and with it interest in battery-powered motor control.
This trend is stimulating demand for driver ICs capable of driving devices even at the low voltage of 1.8V (0.9V × 2 batteries, whose capacity is reduced by discharge though 1.5V, 1.2V, etc. are initial voltages.).
Until now, the mainstream devices have been H-bridge driver ICs constructed with bipolar transistors, which can achieve stable operation at low voltage. However, problems with this include large current consumption that shortens battery life and increase current losses in ICs, and insufficient motor torque, since the voltage applied to the motor is lowered.
Toshiba’s new dual-H-bridge driver IC uses Toshiba’s specialized DMOS process for low voltage drives to achieve a longer battery life with a stable low voltage operation. Improved motor torque is also realized by reducing IC losses through low on-resistance [3]. The new product is suitable for motor applications driven by relatively low voltage batteries (1.8V to 6.0V).
Main features |
||
(1) | Low current consumption prolongs battery life. | |
(ICC = 0.6 mA (typ.) in operation mode when VM = 3.0V and Ta = 25°C; ICC = 0 µA (typ.) in standby mode when VM = 3.0V and Ta = 25°C) | ||
(2) | Low on-resistance reduces IC losses generated by voltage drops in the motor driver and increases the voltage applied to the motor, contributing to improved motor torque. | |
(Ron = 0.25Ω (typ.) (total of high and low sides when VM = 5V and Ta=25°C) | ||
(3) | Error detection functions for over current protection, thermal shutdown, and under voltage lockout contribute to device safety. | |
Applications |
||
Motor applications driven by relatively low voltage batteries (1.8V to 6.0V), mobile devices (cameras and compact printers) using 3.7V lithium-ion batteries, products for the home, such as gas stoves, smart meters, and electronic locks, toys using two 1.5V dry batteries, and devices using 5V USB power supply. | ||
Main specifications |
||
Product name | TC78H651FNG | |
Power supply voltage
(Operating range) |
1.8V to 6.0V | |
Output current
(Absolute maximum rating) |
1.6A | |
Number of H-bridge channels | 2ch | |
Drive motors |
DC brushed motors (driving two motors is possible.)
|
|
Output on resistance
(total of high and low side) |
0.25Ω (typ.) when VM = 5.0V and Ta = 25°C | |
Detection functions | Over current detection, thermal shutdown, and under voltage lockout | |
Package | TSSOP16 (size: 5.0 mm x 6.4 mm, pin pitch: 0.65 mm) | |
Other features |
Built-in standby function: power consumption is 0μA (typ.)
|
|
Mass production |
June 2018 |
|