Company’s Rail Industry Solution Designed to Meet Requirements for Passenger Trains and Light Rail, With Materials Passing European Standard EN45545-2
FRANKFURT AM MAIN, Germany — (BUSINESS WIRE) — November 19, 2019 — At a press conference at the Formnext 2019 trade fair, Stratasys (NASDAQ: SSYS) announced its Rail Industry Solution to help passenger trains – from long-haul to urban metros – run on time more frequently and potentially save thousands of euros a day. By using its ULTEM™ 9085 resin and Antero 800NA material with Stratasys Fortus 3D printers for production, rail operators will be best positioned to leverage additive manufacturing for the production of spare parts on demand that meet strict government certification requirements for smoke, fire, and toxicity. Both materials have passed the European Union’s Rail Standard, EN45545-2.
This press release features multimedia. View the full release here: https://www.businesswire.com/news/home/20191119005639/en/
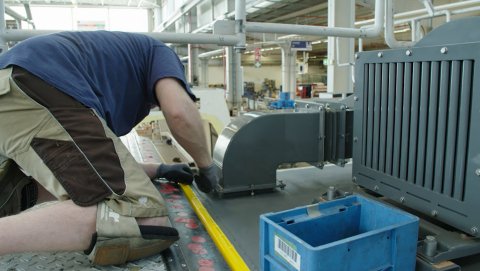
Customized 3D printed air vent system produced by Bombardier Transportation on Stratasys' large-scale F900 3D Printer (Photo: Business Wire).
The Stratasys ecosystem of customers and partners benefiting from the Rail Industry Solution currently includes Angel Trains, Bombardier Transportation, Chiltern Railways, DB ESG, and Siemens Mobility.
Stratasys’ additive manufacturing consultancy, Blueprint, has estimated that for one major U.S. commuter rail service, every day a train set is out of service costs €18,000, and often a single part that would ordinarily cost less than €100 is all that keeps the train from running. Compounding the challenge, the service life of trains is typically 35-45 years making sourcing spare parts a challenge. By turning to additive manufacturing, train operators can get the parts they need within a day or two regardless of the uniqueness of the part or the age of the train car, minimizing time spent in a maintenance yard and dramatically reducing costs.
“In industry after industry, we continue to see organizations discover how additive manufacturing improves customer service, streamlines maintenance and operating costs, and helps engineer lighter, durable products,” Stratasys EMEA President Andreas Langfeld said. “Rail is no exception. The old model of keeping trains running through expensive physical inventory or slow and costly traditional manufacturing is being replaced by digital inventory and on-demand 3D printing. Indeed, this is exemplified by some of the biggest names in European passenger rail.”
Part of Deutsche Bahn, DB ESG, based in Derby, U.K., helps train operators and rolling stock owners keep trains in service by reverse engineering obsolete components. “Additive manufacturing allows us to efficiently produce parts for the passenger environment that are indistinguishable from the existing parts,” said Martin Stevens, Mechanical Engineering Manager at DB ESG. “The Stratasys range of EN45545-2-compliant materials enable us to reverse-engineer parts, such as interior grab handles, with freeform curves that traditionally could only be made with casting or injection molding, without the need for expensive tooling, and with a corresponding reduction in delivery times. Stratasys’ GrabCAD Print software allows us to precisely define the printing parameters, then lock down the print file to ensure consistent parts production across multiple printing bureaus.”
Stratasys rail-qualified materials include ULTEM 9085 resin, a flame-retardant, high-performance thermoplastic that has passed European standard EN45545-2 for all three Hazard Levels – HL1, HL2 and HL3. It features a high strength-to-weight ratio, excellent heat resistance, and high-impact strength. Also included is Antero 800NA, a PEKK-based thermoplastic possessing mechanical properties such as high strength, high heat resistance, toughness and wear resistance. The material is compliant with EN45545-2, permitting it to be used to produce a wide range of components. Both work with Stratasys Fortus 3D printers built specifically for manufacturing and heavy industries, with large build sizes, high part accuracy and repeatability, and compatible with the new GrabCAD Shop software, which streamlines work order management for centralized 3D printing shops.
German manufacturer Bombardier Transportation is using the Stratasys Rail Industry Solution to accelerate the development process of new trains, including 3D printing interior and exterior train parts, such as air ducts, housings and cable holders. “Our goal during the development process for new trains is to speed up the production of project-specific parts that take a while to design,” said André Bialoscek, Head of Vehicle Physical Integration for Bombardier in Henningsdorf, Germany. “While accelerating production, we still need to ensure that total functionality, safety, and repeatability are upheld. With Stratasys’ Rail Solution, we are able to do all those things – it has been a game-changer for our department.”
Angel Trains, one of the U.K.’s leading train leasing companies, is using the Stratasys Rail Industry Solution to manufacture a range of direct replacement parts including passenger arm rests, grab handles and equipment covers. “Sourcing obsolete replacement parts for older train fleets within short timeframes and at reasonable costs is becoming increasingly difficult and presents several challenges for train operators,” said James Brown, Data and Performance Engineer, Angel Trains. “Stratasys Rail Qualified Materials and production-grade Fortus machines enable us to design and manufacture replacement parts quickly and reliably that meet all required railway standards. As such, we’re able to lower costs and lead times while reducing engineering time spent on managing obsolescence issues. This exciting technology gives rail operators peace of mind over their supply chain for older fleets and will ensure improvement to passenger experience in the future.”
Learn more about Stratasys rail solutions and then explore Blueprint’s analysis of the business drivers of 3D printing in light rail applications.
Stratasys is a global leader in additive manufacturing or 3D printing technology and is the manufacturer of FDM® and PolyJet™ 3D printers. The company’s technologies are used to create prototypes, manufacturing tools, and production parts for industries, including aerospace, automotive, healthcare, consumer products and education. For 30 years, Stratasys products have helped manufacturers reduce product-development time, cost, and time-to-market, as well as reduce or eliminate tooling costs and improve product quality. The Stratasys 3D printing ecosystem of solutions and expertise includes: 3D printers, materials, software, expert services, and on-demand parts production. Online at: www.stratasys.com, http://blog.stratasys.com and LinkedIn.
Stratasys and FDM are trademarks or registered trademarks of Stratasys Ltd. and/or its affiliates. ULTEM™ is a registered trademark of SABIC or its affiliates. All other trademarks are the property of their respective owners, and Stratasys assumes no responsibility with regard to the selection, performance, or use of these non-Stratasys products.
Attention Editors, if you publish reader-contact information, please use:
- USA +800-801-6491
- Europe/Middle East/Africa +49-7229-7772-0
- Asia Pacific +852 3944-8888
View source version on businesswire.com: https://www.businesswire.com/news/home/20191119005639/en/
Contact:
Media Contacts
Stratasys Corporate & North America
Craig.Librett@Stratasys.com
+1 612-364-3208
Europe, Middle East, and Africa
Jonathan Wake / Miguel Afonso, Incus Media
stratasys@incus-media.com
+44 1737 215200
Asia Pacific and Japan
Alice Chiu
Email Contact
Mexico, Caribe
Carlos.ramirez@stratasys.com
00+52 (55) 15349791
Brazil, Central America and South America
Erica.massini@stratasys.com
+55 (11) 2626-9229