First International Installations of the Studio System to Include BMW Group, Weir Group, Soprofame, Edalis, Additive Italia, Jade Groupe and More
BURLINGTON, Mass. — (BUSINESS WIRE) — June 20, 2019 — Desktop Metal, the company committed to making metal 3D printing accessible to manufacturers and engineers, today announced it has begun shipping its Studio System™ to customers and resellers throughout Europe. The world’s first office-friendly metal 3D printing system for functional prototyping and low volume production, has met with strong adoption in North America among leading companies, including Ford, Stanley Black and Decker, Google’s ATAP, Goodyear, Owens Corning, and John Zink Hamworthy Combustion. Building on that momentum, the Studio System is now CE certified for international compatibility and being installed at customers throughout Europe, including France, Germany, Greece, Italy, Portugal, Spain, the Netherlands, and the United Kingdom.
This press release features multimedia. View the full release here: https://www.businesswire.com/news/home/20190620005055/en/
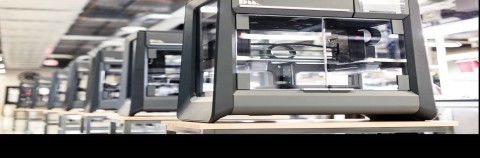
Desktop Metal is now shipping the Studio System, the world’s first office-friendly metal 3D printing system, to companies throughout Europe. (Photo: Business Wire)
“When Desktop Metal first launched, we set forth a mission to fundamentally change how the world designs and produces metal additively manufactured parts, from functional prototyping to mass manufacturing,” said Ric Fulop, CEO and co-founder of Desktop Metal. “We have been delivering on that vision throughout the U.S. and Canada, and are now ready to step onto the global stage to further accelerate our business expansion and answer the impressive demand of the European market.”
In anticipation of the international expansion, Desktop Metal has been working for more than a year with a select group of strategic customers as early stage evaluators of its technologies. These strategic partners have been a source of key user feedback on benchmark parts, materials, training and system usage. International customers of the Studio System span multiple industries, including automotive, education and defense, as well as service providers of luxury brands and consumer products. Leading companies, including BMW Group in Germany; Politecnico Di Milano, one of the largest technical universities in Europe and Additive Italia srl (Add+It) in Italy; EGIBIDE and Centro Avanzado de Fabricación (IMH) in Spain; Edalis, Soprofame and MSA in France; Weir Group and the city of Sheffield in the UK; Jade Groupe of Portugal, which specializes in metal parts production for the luxury fashion world; and BAZIGOS of Greece, a manufacturing firm specializing in high precision components, are among the first customers to benefit from the ease of use and accessibility provided by the Studio System.
Studio System for Metal Prototyping and Low Volume Production
The
Studio System is designed to make metal 3D printing more accessible,
enabling design and engineering teams to print metal parts faster,
without the need for special facilities, dedicated operators, or
expensive tooling. The three-part solution, including printer, debinder
and furnace, automates metal 3D printing by tightly integrating through
Desktop Metal’s cloud-based software to deliver a seamless workflow for
printing complex metal parts in-house—from digital file to sintered part.
To date, Studio Systems worldwide have fabricated more than 10,000 parts, with applications ranging from functional prototyping of extruder nozzles and shock absorber pistons; to jigs & fixtures, including robotic end effectors and smartphone fixtures; to manufacturing tooling of zipper molds inserts and extrusion dies; and low volume production of gears and motor mounts. Each of these benchmark parts has shown drastic cost reduction – some by as much as 90 percent relative to machining and selective laser melting (SLM) – as well as speed in fabrication, producing parts in days instead of weeks or months.
Early Customer Applications and Highlights
Customer feedback
on benefits companies can now achieve include:
- Built to Scale: The Studio System offers a 10 times larger sintering volume than competitive systems, which enables cost-effective, low-volume production of metal parts. One Studio furnace supports up to five printers, allowing for batch processing for high throughput.
- Superior Parts: Mechanical properties, material properties, surface quality, feature fidelity, geometry, size, dimensional accuracy – the Studio System considers each of these critical factors with expertly engineered features to ensure great parts.
- Safe for the Office: A key differentiator of the Studio System is that it prevents exposure of solvents to users and does not require external ventilation. The system is designed for use in a range of environments — office, lab, shop — making it easy for any engineer to make metal parts in-house.
France:
- “Edalis, a unique kind of industrial concierge, is a major player of 3D printing services in France, from project study to production,” said Nicolas Blanchard, Managing Director at Edalis. “Our design office and workshops allow us to deliver final end-use parts. Our choice to invest in the Desktop Metal Studio System is based on our willingness to continue innovating for our customers, complement our quality equipment installed base and be very agile thanks to the easiness and flexibility of this tool.”
- Soprofame is a machining, precision engineering and additive manufacturing expert, for plastic and metal. “We decided to invest in the Desktop Metal Studio System in order to provide our customers a complementary solution to our machining expertise,” said Jean-Baptiste Frenel, Director at Soprofame. “This innovative technology will allow us to answer our customer needs with more effectivity and reactivity, bringing a real value added to our know-how and a differentiating offer in an ever-changing market.”
- Founded in 1985, MSA is a recognized expert of boilerwork, welding and public lighting. “ MSA chose to invest in Additive Manufacturing technologies to diversify these offerings and better answer customer solutions,” said Martial Champion, CEO of MSA. “The Studio System will allow us to produce in-house metal parts with a variety of complexities, with more speed and flexibility. Among other AM solutions, the Studio System was the easiest to implement and safer for our operators.”