LEMONT, Ill. — (BUSINESS WIRE) — April 13, 2023 — In traditional manufacturing, components are created out of larger blocks of source material (such as steels) and the unused excess materials or the machining scraps are thrown away or recycled. In 3D printing projects, spools of nylon-like threads or metal wires – or powdered metals – can be fused together, layer by layer, into usable components of almost any variation imaginable.
This press release features multimedia. View the full release here: https://www.businesswire.com/news/home/20230413005541/en/
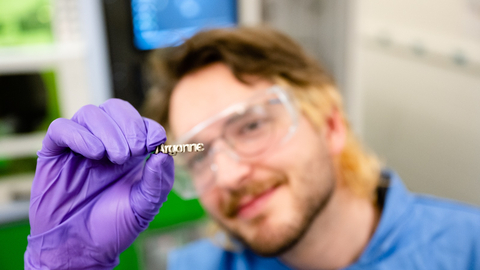
U.S. DOE’s Lab-Embedded Entrepreneurship Program, which funds Argonne’s Chain Reaction Innovations program, helped Phase3D’s Niall O’Dowd connect with resources and experts to develop clean energy through high tech. (Image by Argonne National Laboratory.)
Until recently, most 3D printed metal components were simply prototypes. But increasingly, companies want to 3D print commercial parts for products that range from use in space rockets to orthopedic devices. Scientists at the U.S. Department of Energy’s (DOE) Argonne National Laboratory are working with entrepreneurs to tap even more benefits from high-quality 3D printing with metal. They are looking at how it can help U.S. industry decarbonize manufacturing processes and help in the fight against climate change.
“Metal additive manufacturing (AKA 3D Printing) is a more sustainable way to make parts because it generates less waste,” explained Niall O’Dowd, whose start-up company Phase3D is part of Argonne’s Chain Reaction Innovations (CRI) program, a two-year fellowship for innovators focused on clean energy and science technologies. The DOE funds programs like CRI at national laboratories through its Lab-Embedded Entrepreneurship Program. “By inspecting parts at the time they are printed and reducing the overall materials used compared to conventional machining, we can improve processes and reduce greenhouse gas emissions.”
O’Dowd designed optical monitoring software and hardware to inspect the quality of printed parts during the 3D printing process. Using structured light, the technology digitally measures the height of what seems like impossibly thin layers of metal to detect defects early on. This can help a manufacturer stop a build mid-process, adjust for any problem and resume successful 3D printing.
Xuan Zhang, an Argonne principal materials scientist, helps O’Dowd interface with DOE and the American Society of Mechanical Engineers to ensure printed materials meet certification requirements. She has also been known to help him sabotage his builds. By deliberately introducing a defect, this helps O’Dowd test the detection capabilities of his technology.
As 3D printed parts make their way out of plastic novelties and into jet engines and other complex designed parts, the need for data that testifies to the quality of such parts will only grow.
“What we really want to achieve is a so-called ‘ideal build,’ where everything is perfect and there shouldn’t be any performance issue,” said Zhang.
View source version on businesswire.com: https://www.businesswire.com/news/home/20230413005541/en/
Contact:
Christopher J. Kramer
Head of Media Relations
Argonne National Laboratory
media@anl.gov
Office: 630.252.5580